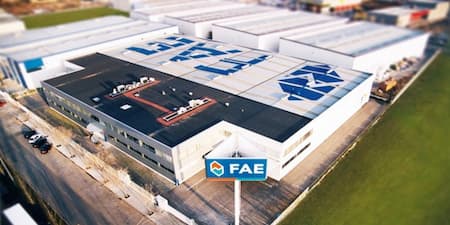
FAE Francisco Albero S.A.U. – Production time optimization system using motion study and a collaborative robot.
Technological solution capable of speeding up the working times of an industrial plant by means of motion study and a collaborative robot.
ARTIFICIAL INTELLIGENCE | BIG DATA | COLABORATIVE ROBOT | MOTION STUDY
INDUSTRIAL STARTING POINT
The project arise from the need of FRANCISCO ALBERO (FAE), as a multinational company, to optimise the production process while minimising occupational hazards through collaborative robots.
Context of the problem was:
- Operators perform a series of movements on the assembly line that require the use of both hands.
- One hand is always free.
- Movements to be addressed are: turning and welding (with the right hand) and picking up and releasing (with the left hand).
In conclusion, it is determined that FAE needs a data processing system to speed up production movements and to apply rules to the collaborative robot.
SOLUTION
The solution adopted by FAE was the development of an industrial solution with an artificial intelligence learning programme.
Initially, the project consisted of collecting data to carry out a series of laboratory tests with the information gathered. For this, GFFSM algorithm was used because it allowed three different activities to be selected and to fluctuate between one and the other when fuzzy logic rules were met.
GFFSM algorithm has a genetic component capable of optimising parameters and complying with the activity exchange rules. These parameters allow to define for each rule what is defined as low, medium and high movement. This optimisation conflicts with the high computational and temporal cost it requires.
In order to reduce input dataset, a genetic feature selection algorithm, known as the Wrapper Algorithm, was also developed.
This method uses an input dataset and selects an optimal subset of several features. Based on the previously developed GFFSM system, we implemented a system that allowed selection from the initial set of selected and pre-filtered variables by means of Feature Selection.
Critical to the implementation of these systems was the labelling of the different states, and although the system already recorded them automatically, manual adjustment was required because the activities are very fast and the operators identifying them could not reach those speeds. They were then visually grouped taking into account the data collected:
- Mount
- Turn
- Place
- Weld
- Release
The right hand implements activities that the left hand did not perform, being these:
- Mount
- Turning
- Welding
While the left hand performed the following activities:
- Riding
- Place
- Release
The only common activity in both hands is mounting as the interaction between both hands is required to thread the tubes into the NTCs.
IMPLEMENTATION
Implementation of the solution was carried out in several milestones, based on a first preparatory phase consisting of:
Determination of functionalities required by the prototype and necessary tools.
And a series of successive activities in the execution of the solution:
- Analysis of the type of movements carried out in manufacturing.
- Data collection in order to apply behavioural rules to the collaborative robot.
- Development of a genetic algorithm capable of determining these rules in the shortest possible time.
- Laboratory tests.
- Data tagging.
- Testing and validation of the system.
ROLE OF ITCL
- ITCL has accompanied FAE in this technological process, from the outset providing fundamental advice on collaborative learning between the operators and the robot and the use of artificial intelligence techniques.
- Once the field of experimentation had been determined, ITCL designed the entire technological basis for the implementation of the algorithms, and proposed the work scenarios, both in ITCL for the laboratory tests and in FAE’s facilities for the tests in the real environment.
- ITCL’s role involved working in collaboration with FAE, from the identification of the problem, the search for solutions through artificial intelligence and the development of experiments and testing of the solution obtained.
CHALLENGES FACED
- To introduce artificial intelligence techniques in the learning of a collaborative robot.
- Capture the movements of operators in their work environment.
- Define movements made by the operators that would allow them to interact with collaborative robots.
- Define the most appropriate algorithms for the specific problem of manipulation in the assembly of parts.
- Program learning by means of artificial intelligence algorithms.
- Adjust the models and validation of the robot states according to the variables identified.
IMPROVEMENTS ACHIEVED
- To achieve the correct operation of the robot both in the simulation phase and in the laboratory phases with the collaborative robot.
- Characterise operator activities in order to determine the rules that define each of the relevant and critical movements so that the assembly line does not come to a standstill.
- Capture real-time acceleration sensor data from devices placed on the wrists of the operators and from a communication gateway between the sensors and the robot that allows real-time communication of movement commands to the robot.
- To comply with the set of rules programmed to synchronise human and robot movements.
- To be able to give orders to the robot depending on the state and variables defined in the collaboration process.
- Develop the necessary algorithms to incorporate learning through artificial intelligence.
- Achieve an assistance system for the assembly of manufacturing orders using collaborative robots.
- Achieve a simulation environment that allows to see the existing collaboration between the operators and the robot.
- Define activities or positions that allow collaborative work between the robot and the assembly personnel by means of a measuring device using accelerometers.
PARTICIPATING COMPANIES AND PROFILE
CONTACT PERSON:
Silvia González, Head of Artificial Intelligence – silvia.gonzalez@itcl.es
ASTICULOS RELACIONADOS:
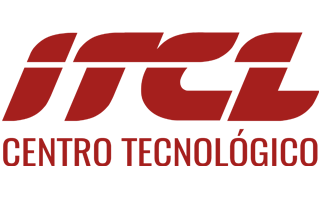