ENERGY SYSTEMS AND MODELS
The ENERGY MODELS AND HYDROGEN ENGINEERING (ENERyH2) unit specializes in the digitalization, analysis, modeling, and optimization of energy systems across various sectors. This includes aspects related to hydrogen engineering and the development of digital twins that replicate energy systems for optimization, simulation, and analysis. Our focus is on applying advanced tools for energy management in industrial environments, buildings, and new energy paradigms such as energy communities and green hydrogen.
Our mission is to design, develop, and implement digital tools and models for the diagnosis, monitoring, simulation, and optimization of industrial and energy facility performance. We seek innovative solutions to improve performance, efficiency, and sustainability in energy management, including aspects related to decarbonization.
Our main goal is to enhance the competitiveness of production sectors by improving energy management, promoting the integration of renewable energy sources, decarbonization, and the energy transition.
R&D CAPABILITIES IN ENERGY AND HYDROGEN
Energy auditing and data-driven optimization
Evaluation of energy consumption in infrastructures through audits, on-site measurements, and characterization of industrial processes. This includes the collection, analysis, and advanced processing of energy data to identify savings and efficiency opportunities.
Modeling and intelligent control for energy efficiency
Application of AI-based models and control algorithms to predict, optimize, and improve energy performance in industrial facilities, including industrial refrigeration systems.
Digitalization and Energy Management Systems (EMS)
Support in defining requirements and launching EMS. Implementation of digital tools for monitoring and optimizing the performance of energy systems.
3D design and development
Creation and integration of three-dimensional models for the design of industrial processes, incorporating physical simulations and finite element analysis to validate and optimize technical proposals.
Development and deployment of digital tools and control systems
Implementation of advanced energy control solutions in buildings using IoT sensors for real-time consumption monitoring. Integration of EMS for automatic parameter adjustment and system optimization, enhancing efficiency and sustainability through renewable energy hybridization and storage proposals.
Digital twin
We design, implement, and validate digital twins for energy systems to improve efficiency, sustainability, and resilience. From physical modeling to simulation and integration with control systems, our solutions optimize decision-making, operational performance, and environmental impact.
System actuation and control
Implementation of advanced energy control solutions in buildings using IoT sensors for real-time monitoring. Integration of EMS for automatic parameter adjustment and system optimization, enhancing efficiency and sustainability through renewable energy and storage hybridization proposals.
Hydrogen value chain
We address the green hydrogen value chain from production using renewable energy, through compression, storage, and distribution. We study the optimization of hydrogen use in energy and transport networks, contributing to industrial decarbonization and facilitating its integration into sustainable and flexible energy systems.
OUR TEAM
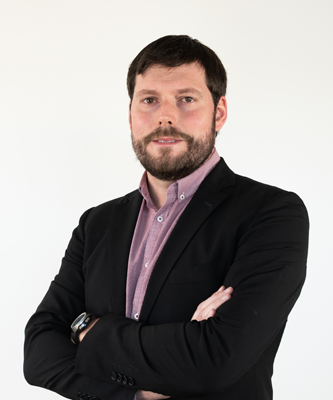
The research group is made up of senior and junior researchers who are continuously seeking innovation in energy management and efficiency systems.
David González
Principal Investigator of the Energy Systems and Models Group
Industrial Technical Engineer, specializing in Mechanics, with experience in energy efficiency. He has conducted energy audits in industrial and service companies in Castilla y León and developed technical documentation for online training. He participated in the European project COOL-SAVE, aimed at reducing energy consumption in industrial refrigeration.
He is a specialist in energy efficiency and collaborates on optimization projects and European R&D&I initiatives.
Javier González
Project Manager for Industrial Refrigeration
He has built his career around modeling industrial systems to improve efficiency and energy management processes, focusing on industrial refrigeration generation technologies. For over 10 years, he has specialized in monitoring, managing, controlling, and optimizing the energy use of machine rooms in leading industrial refrigeration companies.
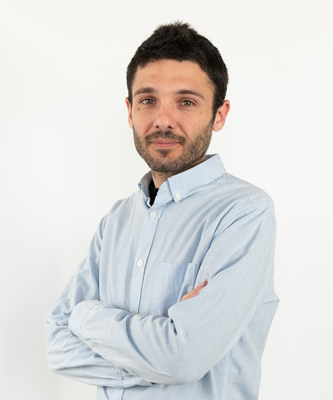
RESEARCH PROJECTS
European AI4CI Master Artificial Intelligence for Connected Industries
The AI4CI project aims to support European educational institutions in creating a program focused on the application of Artificial Intelligence to Connected Industries.
AI4SwEng – AI Engineering Suite to support Agile Efficient Software Engineering
AI4SWEng boosts agile software development through AI, delivering tools for code generation, automated testing, security, and regulatory compliance.
ICONICA: Research in Safe, Intelligent, Connected and Autonomous Driving
The project investigates solutions for connected and autonomous vehicles, focusing on V2I and V2V information exchange using 5G communication networks, which offer high speed and ultra-low latency.
Duration: October 2024 - December 2025
BIOTECARE – Data-Driven Technological Advancement for the Optimization of Biotechnological, Healthcare, and Care Processes
The project aims to drive research and development of innovative solutions based on data science, AI, and Deep Learning to enhance the integration of medicine with these technologies. This will improve how diseases are diagnosed, treated, and prevented, as well as optimize overall healthcare management and patient experience.
Duration: 2024 - 2026
QuantumCrip – Research on the Ambivalence of Quantum Computing for Solving Optimization Problems and Post-Quantum Encryption
Project Description: The QuantumCrip project encompasses two major lines of research and development. The first focuses on exploring quantum computing algorithms and applications, including their execution on both quantum computers and simulators. The second line...