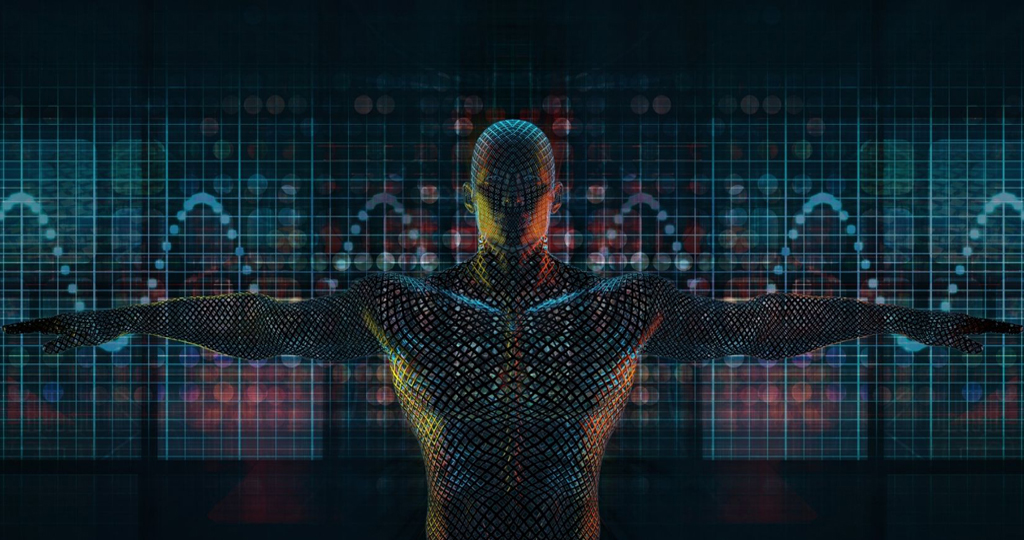
Fandango – Digital Twin in Automotive Manufacturing
Fandango, Digital twin automotive manufacturing is revolutionizing the industry by enhancing efficiency, quality, and maintenance processes. The project leverages this technology to improve supply chain visibility and optimize manufacturing operations.
Fandango is aimed at improving operational efficiency in the automotive components sector by acting on the visibility of information in the supply chain, maximizing product quality and optimizing maintenance processes. It will employ the use of digital twins to detect problems earlier and predict outcomes more accurately than pure simulation models.
What is FANDANGO?
Fandango, a CIEN project funded by CDTI, is aimed at improving operational efficiency in the automotive components sector by acting on three key challenges of the sector such as information visibility throughout the supply chain, maximization of product quality and optimization of processes that do not provide direct value (maintenance).
The FANDANGO project will employ the Digital Twin concept understood as the hybridization of virtual models or simulations with real data captured from assets, processes or product. This concept allows earlier detection of problems and prediction of process results with greater accuracy than pure simulation models.
FANDANGO problem to be solved: Enhance efficiency in automotive manufacturing
Address the development of the digital twin concept from a maintenance optimization point of view with the purpose of:
- Evolve the maintenance strategy from an exclusively preventive strategy to one with focus on condition.
- Acquire more information about the companies’ production processes in order to subsequently optimize them.
Both objectives are of great importance and are already being worked on through the digitalization of the press, but they will receive a major boost through the “FANDANGO” project and the use of the digital twin technology.
Grupo Antolin does not intend to exploit the technology developed and therefore has no commercial objectives, but it will have an indirect economic impact:
- Increased profitability on the lines by reducing the number of both scheduled and unscheduled stops.
- Increased profitability in the plant by optimizing resources allocated to machine maintenance.
- To be a pioneer in the implementation of digital twins in its processes and position itself as a leading company in its sector.
FANDANGO Objectives
In the FANDANGO project 3 use cases are made explicit in addition to a transversal line of action. In the following figure we can see how Grupo Antolin and the rest of the collaborating companies participate.
Use case 2: Maintenance optimization, is oriented to demonstrate the maintenance optimization functionalities included in the suite. The main responsible of the use case is Grupo Antolin and will apply the functionalities to two plastic injection molding machines for manufacturing interior door panels and to a waterjet cutting cell for ceiling panels.
In the use case, the CBM approach chosen in the FANDANGO project will be demonstrated by performing RAMS analysis on the chosen machines and then integrating predictive maintenance services to detect the most relevant failure modes of these machines.
For the correct execution of the project, a project activity management structure has been defined which divides the work to be carried out into 5 main activities or work packages as shown in the following figure. Grupo Antolin participates in all the work packages.
- Definition of use cases and technical specifications that will work on the definition of the conditions that guarantee that, on the one hand, the technical developments of the project meet the requirements of the use cases and, on the other hand, follow homogeneity criteria that allow its future adaptation to other fields of application in a simple way.Below are 3 technical work packages that deal with the development of technology for each of the layers of the intelligent system model:
- Sensorization and data capture: this work package will include all activities oriented to capture real-time information from assets: machines, tooling, quality control systems.
- Interconnection of systems and exchange of information in the value chain: this work package will work on the technologies necessary for the collection and correct management of traceability information both within the organization and throughout the value chain.
- Hybrid models and development of digital twins: this work package will work on the virtual domain intelligence layer. Specifically, research will be done on data analytics techniques for the implementation of condition-based maintenance and optimal process control for quality maximization.
Finally, the modules developed in the three previous technology work packages will be integrated into:
- Technological integration and evaluation to build the three use cases described above. This will allow validation and evaluation of the results obtained in the project.
Technical tasks to be developed by the ITCL Technology Center
- Sensorization and data capture
- Reference architecture design for data capture. Collaborates in the definition, design and monitoring of the data capture architecture with special attention to Big Data and IIoT requirements.
- Hybrid models and development of digital twins
- Diagnostic and prognostic algorithms for maintenance. Collaborates in the design and verification of predictive/prescriptive models of the maintenance use case.
FANDANGO duration
2018 – 2022
Cooperation project with:
Financed by:

Contact person:
Javier Sedano – javier.sedano@itcl.es
Silvia González – silvia.gonzalez@itcl.es
Discover more projects that integrate Electronics and Artificial Intelligence, contact us and explore how these technologies can transform your industry.
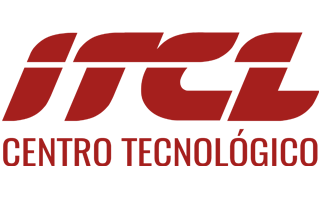