Specific solution for cold Industrial Energy Efficiency
The solution that has been designed by the Technological Institute of Castilla and Leon (ITCL) to improve the energy efficiency of the Industrial Refrigeration plants, especially in Ammonia (NH3) or CO2 plants, is steadily paying off.
This solution, already implemented in several important reference customers, mainly in the food sector, with important facilities for the manufacturing and storage of frozen products, is providing excellent energy savings, which are directly transformed into economic savings.
As the best example we may take one of our best customers, GAMBASTAR, located in Burgos, Spain, and participated by Prim7stars Group, a leading European seafood company. Gambastar is marketing an annual output of 10,000 tons of shrimps and prawns, 70% of this amount is processed within its manufacturing facilities in Valdorros (Burgos). The raw material, which is received frozen, must be warehoused and sold frozen (mainly) as well.
GAMBASTAR, with ITCL collaboration, has been one of the pioneers in adapting its facilities and the way of working with the plant refrigeration compressors, with the target to maximize the efficiency of their freezing equipment, a key aspect in their market as it directly affects to the costing of their products and, therefore, to the competitiveness of the company.
GAMBASTAR won the “2015 FAE Innovation” award, after introducing and adapting specific research techniques developed by the ITCL Energy Department into their freezing plant for mechanical compression production of cold through ammonia (NH3), reaching at this first stage an amount of energy savings of 15%, by regulating the compressors and other operating equipment parameters after the implementation of an expert Supervisory Control System designed by the R+ D+ Energy Department of ITCL.
Although the forecasts were already optimistic, it was intended to achieve a percentage of energy savings of 21%, the current results are even much better, achieving some months a 40% saving in energy consumption, with an average saving of 30% after the application of some improvements in the operating configuration of the freezing plant, as a result of improving the use of the tool and the close collaboration between the technical area of ITCL Energy Department and GAMBASTAR.
GAMBASTAR continues with their commitment to innovation, and they are working in new projects that target improvements in production processes lines and the quality of the products processed. In addition, they will continue optimizing their energy consumption management, which will help to fulfill one of its main strategic challenges right now, which is to improve the competitiveness of operations, while working in parallel in markets and products diversification.
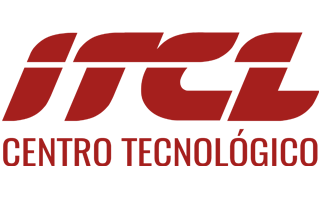