INDUSTRIAL ICT AND DIGITAL TWINS
The Information and Communication Technologies (ICT) Unit aims to facilitate and drive the digital transformation of our clients, especially in the industrial sector and small to medium-sized enterprises. Based on our understanding of their production processes, we provide technological solutions that improve efficiency, competitiveness, and sustainability, adapting to the specific needs of each project and organization.
We are part of a technology center with a strong focus on innovation, allowing us to work closely with other highly specialized departments such as Artificial Intelligence, Applied Electronics, Computer Vision, and Virtual Reality. This cross-disciplinary collaboration enables us to bring the knowledge developed by our colleagues into tangible, real-world solutions that deliver high added value to our clients.
Our team handles the entire lifecycle of each project: from functional analysis, planning, software development and deployment, to commissioning and client follow-up.
We work with a focus on innovation, quality, and continuous improvement. Our mission is to align available technologies with our clients’ business goals, turning ICT into a true driver of change and growth.
The research group on Digital Twins and Advanced Simulation works on the design, development, and implementation of digital models that replicate the behavior of physical systems in real time. This research area combines physical modeling, numerical simulation, data science, and information technologies to support decision-making and optimize the performance of industrial, energy, and environmental processes.
The main objective of the group is to support the digital transformation of industry through the deployment of digital twin solutions capable of efficiently monitoring, predicting, and controlling complex systems. These models allow for scenario analysis, failure prediction, improved maintenance, and cost reduction, thereby enhancing the sustainability and competitiveness of organizations.
The group has solid experience in the development and integration of digital twins across sectors such as energy, water, industry, and hydrogen. It works with modeling tools and languages like Modelica and co-simulation standards such as FMI, integrating models with web environments, industrial control systems, and real-time visualization platforms such as dashboards or VR/AR solutions. The approach is multidisciplinary, covering everything from thermal and mechanical processes to hydraulic, electrical, and biological systems.
ITCL has infrastructure prepared for the development and validation of digital twins, including test benches, IoT systems, simulation servers, and integration platforms with real data. Additionally, it collaborates with companies, research centers, and universities in national and international projects, generating solutions tailored to the specific needs of each use case.
The group specializes in the development of interconnected digital ecosystems, where sensors, predictive models, and visualization platforms work together to enable a new level of insight and control over physical systems.
R&D CAPABILITIES IN ICT
Our unit has extensive experience and a practical approach to the implementation of technological solutions for industry and SMEs.
One of our unit’s core values is customer orientation. Every solution we develop begins with active listening and a deep understanding of the client’s processes. Only in this way can we design technological tools that truly add value, integrate naturally into their operations, and help improve efficiency and decision-making.
These are our main areas of activity:
Digitization of Plant Production Processes
We design and implement solutions that enable the control, optimization, and monitoring of on-site production processes. Our key tools include:
• MES (Manufacturing Execution System) for managing production operations and real-time plant control. Its main objectives are:
o Visualizing key indicators such as performance, availability, and quality (OEE).
o Monitoring the status of manufacturing orders.
o Logging incidents and downtimes manually, or justifying those recorded automatically.
o Controlling batch traceability, from raw materials to finished product.
o Managing work instructions and operational documentation digitally.
o Connecting with ERP systems to keep planning aligned with execution.
• Quality Control Software, integrating automatic records and digital inspections.
We offer a fully configurable module that allows clients complete flexibility to create new quality controls as needed.
• CMMS (Computerized Maintenance Management System) for managing preventive and corrective maintenance.
Designed especially for small and medium-sized companies with limited maintenance staff.
It is integrated with production and energy systems, enabling companies to plan and optimize maintenance processes while minimizing the impact on production.
• WMS (Warehouse Management System) and internal logistics, to improve stock and material flow management.
It provides real-time information on receiving, dispatching, and inventory levels. All this data can be connected to the company’s production systems, CMMS, and ERP to enhance control over supply, movement, and resource needs.
• EMS (Energy Management System) — an energy monitoring and control system that offers a detailed view of process consumption and its optimization.
This tool is also connected to other systems such as production control and maintenance management.
• Production Sequencers that assign and order operations based on resource availability or delivery priorities.
They help optimize plant workload and enable agile responses to unexpected events or changes in demand.
System Integration
We connect our solutions with the client’s existing systems to ensure a continuous flow of information, avoid duplication, and enable data-driven decision-making based on consistent and up-to-date information. We work with:
-
ERP systems (such as SAP, Navision, Odoo, Expertis, etc.)
-
APIs and web services for bidirectional integration
-
Databases from other company tools
-
Commercial devices (e.g., attendance systems, etc.)
Data Capture on the Shop Floor
We collect real-time data from various sources, adapting to the client’s technological environment:
-
Existing SCADA systems and PLCs
-
Commercial sensors (temperature, humidity, energy consumption, etc.)
-
Custom-developed sensor systems, integrable with our platform and other technologies within the center
Analytics and Business Intelligence (BI)
Each of our solutions includes data processing and indicator visualization tools that support real-time decision-making:
-
We can connect our solutions to other data sources to generate KPIs that integrate production, energy, maintenance, planning (ERP, CRM), or any other key business indicator.
-
We create custom dashboards, KPIs, and dynamic reports. The tool also includes a BI module that allows clients to develop their own reports and indicators.
-
We develop artificial intelligence algorithms to enable efficient data usage and provide guidance for Big Data needs. We apply predictive analytics techniques to anticipate failures, deviations, and improvement opportunities.
Custom Applications
We develop solutions tailored to each use case, whether for shop floor users, technical staff, or management profiles:
-
Native mobile applications for Android and iOS
-
Cross-platform web applications, deployable on dedicated servers, contracted services, or in the cloud (AWS, Azure, etc.), adapting to the client’s preferences
Integration with Advanced Technologies
We work in coordination with other technological units within the center to offer innovative, high-value-added solutions:
-
Integration with AI Agent technologies (LLMs) to automate information extraction from documents (orders, invoices, etc.)
-
Process automation with RPA, reducing repetitive tasks and improving operational efficiency
-
Interactive visualization of 3D models, especially useful in training, maintenance, or engineering environments
R&D CAPABILITIES IN DIGITAL TWINS
Digital Model Integration
-
Adaptation and integration of physical models into client architectures, both IT and OT
-
Connection with industrial control systems (PLCs, SCADA), IoT platforms, and databases
-
Modular deployment via APIs, containers, and interoperability standards such as OPC-UA or FMI
-
Synchronization of models with real data, in real-time or delayed, for validation and monitoring
-
Applications: integration of physical models into SCADA environments, synchronization of plant data with simulations, connection with energy management system
Deployment of Digital Twins at the Client Site
-
Development of turnkey solutions tailored to the client’s use case and technological environment
-
Installation on cloud, edge, or private network infrastructure, with full support for commissioning
-
Customization of interfaces, dashboards, and 3D or VR visualizations based on the end-user profile
-
Training, functional validation, and technical support during the operation of the digital twin
-
Applications: operational digital twins in water treatment plants, food industry facilities, or hydrogen installations for monitoring, optimization, and diagnostics
Physical Modeling and Multipurpose Simulation
-
Development of physics-based models using equations in Modelica and standards like FMI
-
Simulation of thermal, hydraulic, electrical, mechanical, or biological systems
-
Evaluation of different operating conditions and analysis of “what-if” scenarios
-
Model validation using historical data, sensor readings, or test bench results
-
Applications: optimization of thermal cycles, simulation of hydraulic networks, evaluation of biological reactor behavior
Process Optimization and Operational Efficiency
-
Performance analysis of facilities using connected models
-
Parameter tuning, control strategies, and operating modes to improve technical and economic KPIs
-
Identification of critical points, efficiency losses, or overdimensioning
-
Integration with energy management platforms or decision-support systems
-
Applications: reducing energy consumption in chillers, improving performance in hydrogen systems, fine-tuning water treatment processes
Predictive Maintenance and Intelligent Diagnostics
-
Asset monitoring by comparing simulated models with real-world data
-
Early detection of deviations, anomalies, or performance degradation
-
Support for maintenance planning and reduction of unplanned downtime
-
Development of hybrid physical-data digital twins for critical assets
-
Applications: fault detection in compressors, performance assessment of pumps, diagnosis of thermal variations in heat exchangers
Technical Training and Safe Validation
-
Generation of training scenarios in virtual or augmented environments
-
Simulation of critical operations without risk to the facility
-
Validation of new control modes and configurations prior to deployment
-
Integration of real-time data for contextualized training
-
Applications: VR-based operator training for WWTPs (Wastewater Treatment Plants), PID controller validation in pumping systems, personnel training in hydrogen plants
Industrial Integration and Interactive Visualization
-
Connection to PLCs, SCADA, databases, or IoT platforms using OPC-UA, MQTT, REST, etc.
-
Visualization through custom dashboards, 3D displays, or immersive environments (Unity, Unreal)
-
Deployment on cloud, edge, or private networks based on client requirements
-
Integration into IT/OT architectures using containers, APIs, and interoperability standards
-
Applications: web-deployed twins for remote monitoring, model integration into SCADA systems, interactive 3D visualization of asset status
OUR TEAM
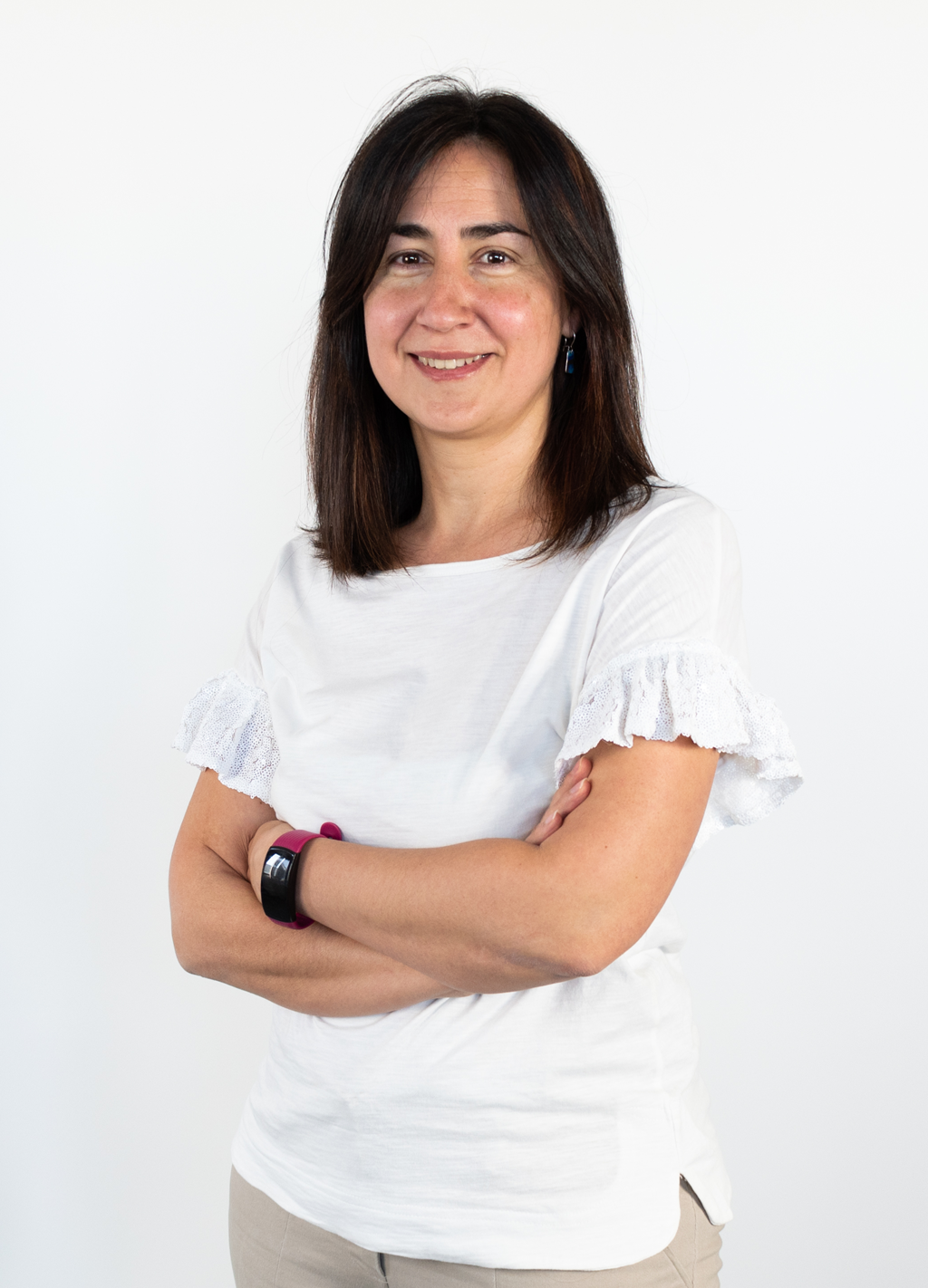
The unit is made up of a multidisciplinary, proactive team focused on continuous improvement, with the ability to adapt to constantly evolving technological environments. It combines technical and analytical profiles with skills in development and support, working collaboratively with other departments to deliver effective solutions aligned with the company’s objectives.
Sonia Rey Osorno
Head of the Industrial ICT Unit
A graduate in Mathematics from the University of Valladolid, she leads the Information and Communication Technologies (ICT) Department at ITCL, bringing over 20 years of experience in the sector. Throughout her career, she has managed technological projects of various scopes, focused on digital transformation and the optimization of production processes.
RESEARCH PROJECTS
ICONICA: Research in Safe, Intelligent, Connected and Autonomous Driving
The project investigates solutions for connected and autonomous vehicles, focusing on V2I and V2V information exchange using 5G communication networks, which offer high speed and ultra-low latency.
Duration: October 2024 - December 2025
BIOTECARE – Data-Driven Technological Advancement for the Optimization of Biotechnological, Healthcare, and Care Processes
The project aims to drive research and development of innovative solutions based on data science, AI, and Deep Learning to enhance the integration of medicine with these technologies. This will improve how diseases are diagnosed, treated, and prevented, as well as optimize overall healthcare management and patient experience.
Duration: 2024 - 2026
SOFIA – Enhancing Productivity in the Software Development Industry through the Use of Reliable AI
Research in an ecosystem of applications to enhance productivity in the software development industry through intensive use of reliable AI throughout its lifecycle
Duration: 2024-2026
AI4HOPE – Artificial Intelligence based health, optimism, purpose and endurance in palliative care for dementia
AI4HOPE focuses on implementing an Advanced Care Planning System for dementia patients and caregivers, integrating emotion regulation and pain management with AI models to improve care while recognizing dementia as a life-limiting disease.
Duration: 2024-2027
Intelligent cybersecurity countermeasures for the network of the future – CICERO
Development of information processing systems to identify and reduce system and network vulnerabilities, based on the application of signal and data security technologies.
Duration 2023-2025