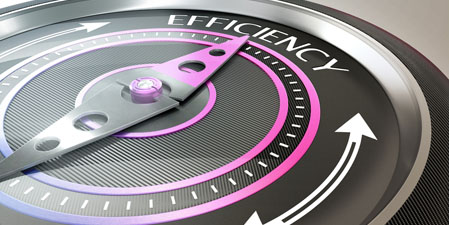
PROEFI-AIRE – Enhancing Energy Efficiency in Compressed Air Systems
PROEFI-AIRE, energy efficiency in compressed air systems is crucial for reducing industrial costs and improving performance. The project focuses on enhancing efficiency thorugh advanced monitoring and predictive tools, addressing the need for better control and cost management in industrial systems.
The project has conducted research on the monitoring and intelligent control of the energy efficiency of vacuum and compressed air installations, key in the industrial sector to reduce inefficiencies in the use of this equipment.
What is PROEFI-AIRE?
In order to reach the foreseen objectives, the project has to go through three phases:
In activity I, a thorough literature review has been carried out, which together with both theoretical and field experience has generated sufficient knowledge to execute the rest of the tasks with guarantees, since the equipment libraries that incorporate the platform for the characterization and diagnosis of facilities have been developed, and the main sources of information existing in the companies have been identified, as well as the key parameters and indicators to be monitored for their correct evaluation.
Through it, it is possible to make a self-assessment of the energy efficiency of the compressed air and vacuum installations of a company, starting from some basic data. The information obtained allows both benchmarking and benchlearning.
Subsequently, activity II has been developed:
Monitoring tools:
With the construction of the platform, for the improvement of energy efficiency in compressed air and vacuum installations, the tools for continuous monitoring and simulation of installations have been developed for the validation of the technical and economic feasibility of the identified improvement strategies
Predictive tools:
With a real-time data capture architecture, a KIT of connections with sufficient capacity to temporarily measure any type of compressed air and vacuum installation, the development of the virtual twins of the installations, the modules for the simulation of improvement actions and the application of Machine Learning and Deep Learning tools.
Once all the above has been established and based on the knowledge generated and the information obtained from Activity I and Activity II, specific calculation procedures have been designed for each tool designed, including expert control tools, predictive maintenance and planning assistant. For this purpose, the processes used have been based on logarithms with learning capacity, adapting their operation to the process characteristics. In addition, level III tools of the PROEFI platform have been developed.
PROEFI-AIRE Problem to be solved: Reduce costs and improve efficiency in compressed air systems
The basic problem we want to solve with this project is the need of companies to know what quantities of compressed air are required at any given time and the amount of energy used to generate that compressed air, and to do so the following problems need to be solved:
- Reducing the energy cost for the use of industrial air.
- To know the real cost of the prediction of industrial air (€/m3), the global efficiency in the production of industrial air (kWh/m3), as well as the efficiency per equipment, pump or compressor.
- It is necessary to determine the origin and weight of the efficiency losses, the main points of loss such as leakage, pressure, sizing and sanitation losses and of course the cost of the loss at each point.
- The quantification of improvements in installations in order to reduce investment costs.
PROEFI-AIRE Objectives:
- Make energy efficiency one more control variable.
- Enable the main teams (compressors) to communicate and collaborate with each other. Collaborative learning.
- Perform and run real-time models simultaneously with the operation of industrial facilities, through virtualization, and under real working conditions.
- Prediction and identification of anomalies and malfunctions, providing control systems with the ability to anticipate / predict critical system failures.
- Giving facilities the ability to self-diagnose.
Expert control systems with learning capabilities, based on industry 4.0 technologies, have made it possible to know the efficiency by equipment or compressor, the overall efficiency of air production, the real costs for the use of industrial air in optimal operating conditions and depending on the needs of production or manufacturing.
PROEFI-AIRE Duration
2018 – 2021
National Project in Cooperation with:
This project is funded through the 2017 call of the Instituto para la Competitividad Empresaruial de Castilla y León de Ayudas en concurrencia no comptetiva destinada a proyectos de I + D aplicada realizados por los Centros Tecnológicos de Castilla y León, co-financed by the European Regional Development Fund (ERDF)

Contact Person:
Javier Sedano – R&D Director at ITCL Technology Center
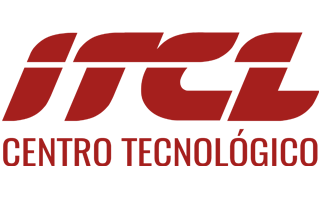