IRC Industrial Refrigeration Control is a smart system specifically developed to improve and optimize industrial cooling facilities control systems.
IRC allows process planners to minimize energy consumption just managing key control parameters in an automatic but also supervised approach.
Recent implantations have reached high saving rates, among 15% and 40% depending on facilities state and working conditions. A typical return of investment period is among 6 and 18 months
Characteristics
- IRC is based on data captured by energy efficiency supervision system from ITCL, IRS
- IRC calculates in real time optimal values for key control parameters, maximizing energy efficiency of the plant while cooling demand is fulfilled.
How it woks
- A smart control system is designed for each company, based on specific requirements of the plant and real climate conditions.
- Smart control system will manage cooling facilities from a control layer above control PLC, modifying in real time control parameters in order to raise global performance for the plant.
- Working conditions are optimized for cooling plants combining specific decision-making algorithms and real time data acquisition system, such as:
— Cooling equipment scheduling
— Start and stop control parameters
— Working parameters values such as pressure and temperature
CASES OF SUCCESS
Case 1: Optimization on control parameters for animal slaughter facilities
- Animal slaughter: 1 MM animals/year
- Cooling production improvement based on a custom-made smart control system
- 20,5% energy consumption reduction for the cooling plant
- Savings: 166.000 €/year // Payback: 6 months
Case 2: Compresors control system optimization
- Shellfish processing company
- Smart control project development
- 42% of annual energy consumption reduction
- Annual savings: 180.000 €/year
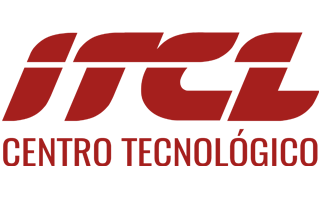