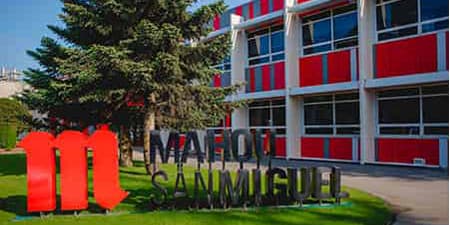
Mahou San Miguel – Ahorro energético en la producción de frío industrial
Reducción del consumo eléctrico destinado a la producción de frío, así como de las emisiones indirectas de CO2, en la planta de Burgos de Mahou San Miguel, mediante la instalación de un Sistema Experto de Supervisión y Control, que modifica de manera dinámica las consignas de la instalación, encontrando el punto óptimo de funcionamiento en cada momento.
MODELADO DE SISTEMAS | IOT | SISTEMAS DE GESTIÓN | DESARROLLO WEB APLICACIÓN DE GESTIÓN
PROBLEMA INDUSTRIAL DE PARTIDA:
La mayoría de instalaciones de frío industrial, entre ellas las de la planta de Burgos de Mahou San Miguel, trabajan con unas consignas de configuración fijas (setpoints de presiones, secuencias de equipos, tiempos, histéresis). No se adaptan, por tanto, a los cambios de condiciones de trabajo tan habituales en el funcionamiento normal de la planta, lo que implica que trabajen, durante largos periodos, lejos de su punto de rendimiento energético óptimo.
Además, la mayoría de instalaciones de frío necesitan un importante impulso para adaptarse a la nueva industria 4.0, lo que exige potenciar la recogida de datos de consumo y rendimiento de la instalación, su integración en un sistema de gestión energética y su análisis avanzado que permita identificar problemas en la instalación, mejorar su rendimiento o, incluso, predecir incidencias.
SOLUCIÓN:
La solución propuesta por parte de ITCL al grupo Mahou San Miguel es doble:
- Desarrollar un Sistema de Supervisión Energética (IRS) de la instalación que permita conocer el COP real de cada compresor y del conjunto de la instalación en cada instante, así como consultar históricos.
- Implantar un Sistema de Control Inteligente de refrigeración industrial (IRC) que actúe automáticamente por encima del autómata de control general, modificando parámetros clave del mismo con el fin de aumentar el rendimiento global de la instalación.
Sistema de Supervisión Energética (IRS)
- Características
Permite calcular el caudal de fluido refrigerante que está moviendo cada compresor, mediante modelos matemáticos (curvas de los compresores desplazadas a su punto real de trabajo en tiempo real) sin necesidad de caudalímetros.
Conocido el caudal, se calcula el rendimiento real (COP) de cada compresor, de cada línea o del global de la instalación. - Funcionalidades
El sistema dispone de una aplicación de monitorización, en formato web, en la que se pueden consultar valores instantáneos e históricos de todas las variables leídas directamente de la instalación, así como de las variables calculadas:- Coeficiente de actuación instantáneo y global de comprensores y líneas.
- Desviación del rendimiento respecto del rendimiento ideal.
- Cantidad de frío producido (kWh frigoríficos).
- Costes diarios asociados a la producción de frío.
- Coste medio de kWh frigorífico producido.
- Desglose de consumo por equipo y periodo.
Figura 1. Sistema de monitorización
El Sistema de Supervisión Energética permite generar informes periódicos, ofreciendo una visión global del funcionamiento de la planta de frío.
- Informes energéticos.
- Informes económicos.
- Informes personalizados en función de las necesidades del cliente.
Figura 2. Informe energético generado automáticamente por la herramienta IRS.
Figura 3. Informe económico generado automáticamente por la herramienta IRS
Sistema de Control Experto de Refrigeración Industrial (IRC)
- Características
El módulo IRC modifica en tiempo real los parámetros óptimos de configuración de la instalación de refrigeración para maximizar la eficiencia energética de la planta para las necesidades de frío reales en cada momento. - Objetivos
Reducir el consumo energético de la planta de frío a través de la modificación de las consignas de la instalación, maximizando el rendimiento instantáneo de los comprensores. - Funcionamiento
El control experto actuará automáticamente por encima del autómata de control general de la planta de frío, modificando parámetros clave del mismo con el fin de aumentar el rendimiento global de la instalación (calculado previamente mediante la aplicación IRS).
Mediante algoritmos de decisión en función de los parámetros de funcionamiento en tiempo real, se optimiza el ciclo termodinámico de refrigeración.
ITCL ha desarrollado algoritmos de decisión propios, basados en Inteligencia Artificial, que consiguen optimizar los siguientes aspectos:- Secuencia de arranque y parada de comprensores
- Secuencia de arranque y parada de condensadores
- Control de presiones experto
- Control de presión de aspiración experto
- Control de parámetros (PID – hiestéresis – tiempos de arranque y parada)
Figura 4. Módulo de control experto
IMPLEMENTACION:
La implementación del desarrollo tecnológico realizado por ITCL para Mahou San Miguel la podemos dividir en diferentes fases:
Fase 1: Instalación de sistema de captura de datos – comunicación con los equipos de refrigeración industrial
En esta fase se analiza la arquitectura de comunicaciones existente en la instalación de frío industrial de Cervezas Mahou San Miguel, así como las necesidades de sensores y equipos a instalar para adquirir los datos en tiempo real de las instalaciones de frío industrial.
Figura 5. Arquitectura de la solución planteada
Fase 2: Puesta en funcionamiento del sistema supervisor (IRS)
Una vez establecida la comunicación con la instalación de frío industrial se instala el software de supervisión de refrigeración. El software se ha diseñado a medida en base a la instalación, definiendo junto con Mahou San Miguel los indicadores a utilizar para evaluar el consumo y eficiencia energética y aquellos a mostrar en los informes periódicos de seguimiento de la eficiencia energética de la instalación de refrigeración industrial.
Durante esta etapa se realizan los siguientes trabajos para la obtención de los indicadores energéticos y económicos en tiempo real, y para la generación de los informes:
- Creación de los modelos matemáticos personalizados de los equipos: Compresores, Condensadores, separadores, …
- Simulación del comportamiento de la instalación mediante el modelo virtual para el análisis del potencial de mejora energética.
Fase 3: Caracterización de la eficiencia energética de la instalación de refrigeración industrial supervisada.
Con los datos adquiridos mediante la herramienta de supervisión energética (IRS) se realizan las siguientes tareas:
- Caracterización de la eficiencia energética de la instalación de refrigeración industrial, durante una serie de meses representativos (dependiendo de la estacionalidad del proceso productivo de la empresa y de las condiciones climatológicas).
- Se establece el valor del COP de referencia de la instalación sobre los que calcular el ahorro y mejora de la eficiencia energética con el uso del módulo IRC.
Fase 4: Desarrollo a medida e implantación del Sistema de Control Inteligente (IRC)
Una vez caracterizada la instalación, se implanta el módulo experto de control de frío industrial (IRC). Dicho control gestiona de forma experta y dinámica la instalación de frío de Mahou San Miguel, de tal forma que el rendimiento energético sea el máximo posible para cada escenario de trabajo de la instalación.
Figura 6. Comparativa entre la instalación Con y Sin control dinámico
* Nota 1 – En la parte superior de la gráfica se observa como varía la presión de alta con el control dinámico (línea azul), frente a una consigna estática (línea roja). En la parte inferior, se calcula el % de mejora obtenido en cada instante comparando los dos escenarios anteriores.
Ahorro energético en la producción de frío industrial 8.
Una vez se el sistema de control experto (IRC) está puesto en marcha, se comienza a generar informes periódicos donde se valida el ahorro energético obtenido en las salas de frío y su conjunto.
Fase 5: Seguimiento durante 24 meses del sistema de Supervisión y Control
Una vez puesta en marcha la instalación con el control experto, se realizan 24 meses de acompañamiento a la instalación, con varios objetivos:
- Garantizar el correcto funcionamiento de la herramienta durante esos meses, así como resolver cualquier incidencia en su manejo.
- Generar e interpretar los indicadores mensuales.
- Garantizar que la instalación mantiene, o mejora, los ratios de ahorro respecto al COP de referencia establecido.
PAPEL DE ITCL:
ITCL ha desarrollado durante años este sistema de supervisión y control de frío industrial, el cual se encuentra implantado en 14 instalaciones, con más de 100 compresores controlados.
Para cada nuevo cliente (Mahou San Miguel), ITCL ajusta los modelos a la instalación real, adapta la aplicación de monitorización y desarrollo los módulos de control experto que optimicen el funcionamiento de la sala de frío.
Además, ITCL mantiene un objetivo de mejora continua de su herramienta, integrando en su aplicación base los desarrollos realizados en cada nuevo proyecto.
RETOS ABORDADOS:
- Calcular el caudal de fluido refrigerante que está moviendo cada comprensor, mediante modelos matemáticos sin necesidad de caudalímetros.
- Implantar un gemelo digital, sobre el que simular diferentes escenarios de configuración, eligiendo e implementando en tiempo real aquellos set-points que mejoren el COP global de la instalación.
MEJORAS CONSEGUIDAS:
Se han conseguido importantes mejoras para Mahou San Miguel:
Monitorización – Industrial Refrigeration Supervision (IRS)
- Conocer y caracterizar la eficiencia energética instantánea y promedio de su instalación de refrigeración industrial en el momento actual.
- Consultar datos históricos.
- Disponer de informes periódicos personalizados para el control de la eficiencia energética.
- Evaluar, de forma continua, el impacto en el consumo energético de acciones de mejora futuras que se puedan llevar a cabo.
- Cuantificar las ineficiencias por compresor en base a desgastes/averías o funcionamiento en puntos fuera de rango óptimo.
Control – Industrial Refrigeration Control
- Disminución del consumo eléctrico para la producción de frío.
- Mejorar la eficiencia energética (COP) de las instalaciones de frío.
- Disminuir las emisiones indirectas de CO2, al reducir el consumo eléctrico de la planta y, con ello, la huella de carbono de su producto.
EMPRESAS PARTICIPANTES:
DATOS DE INTERÉS:
En la siguiente tabla se resumen los hitos principales del proyecto:
Abril 2019 | Inicio captura de datos |
Diciembre 2019 | Fin periodo de caracterización |
Diciembre 2019 | Puesta en marcha Control Experto IRC |
Dic 2019 – enero 2020 | Implantación nuevos variadores. Cambio motor. |
Enero – abril 2020 | Seguimiento y mejora Control |
Abril 2020 – Actualidad | Instalación en funcionamiento |
DATOS E INFORMACIÓN DE RESULTADOS:
Figura 7. Comparativa enre la instalación Con y Sin control dinámico
* Nota 2 – Esta gráfica compara el consumo eléctrico de la instalación Con y Sin Control dinámico para una misma demanda de frío. De esta forma, para una demanda de 4.000 kWhf, la instalación consume aproximadamente unos 3.000 kWh en vez de los 4.000 kWh que hubiera consumido en la situación inicial sin control dinámico.
PERSONA DE CONTACTO:
Diego Martínez – diego.martinez@itcl.es
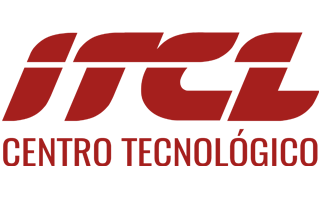